Understanding Force Measurement
Converting mechanical force
A load cell, which is also known as a force sensor or force transducer, is a sensor that measures force by converting the input of mechanical force into the output of an electrical signal. As the force is applied to the sensor, its electrical output signal can be measured, converted, and standardized. The input force can vary between load, weight, tension, compression, or pressure, and it can only be measured by a sensor that is designed to calculate that type of force. (We will break down the different kinds of load cells/ force transducers in the section below.)
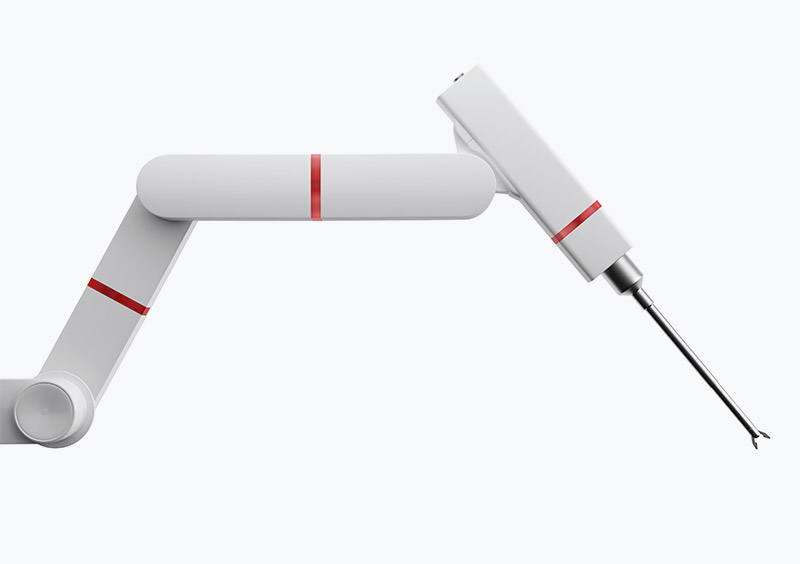
Industries that use load cells
Due to their accuracy, load cells have become an essential element in many industries. Common sectors that rely on high-precision load measurement include automotive, high-precision manufacturing, aerospace and defense, industrial automation, medical and pharmaceuticals, and robotics. The design and development of load cell sensors are continuously evolving. With the current advancements in cobots and surgical robotics, many innovative force measurement applications are emerging, requiring ever more sophisticated force measurement solutions, such as FUTEK’s miniature medical sensors for robotic surgery.