Custom Miniature Reaction Torque Sensor for OEM
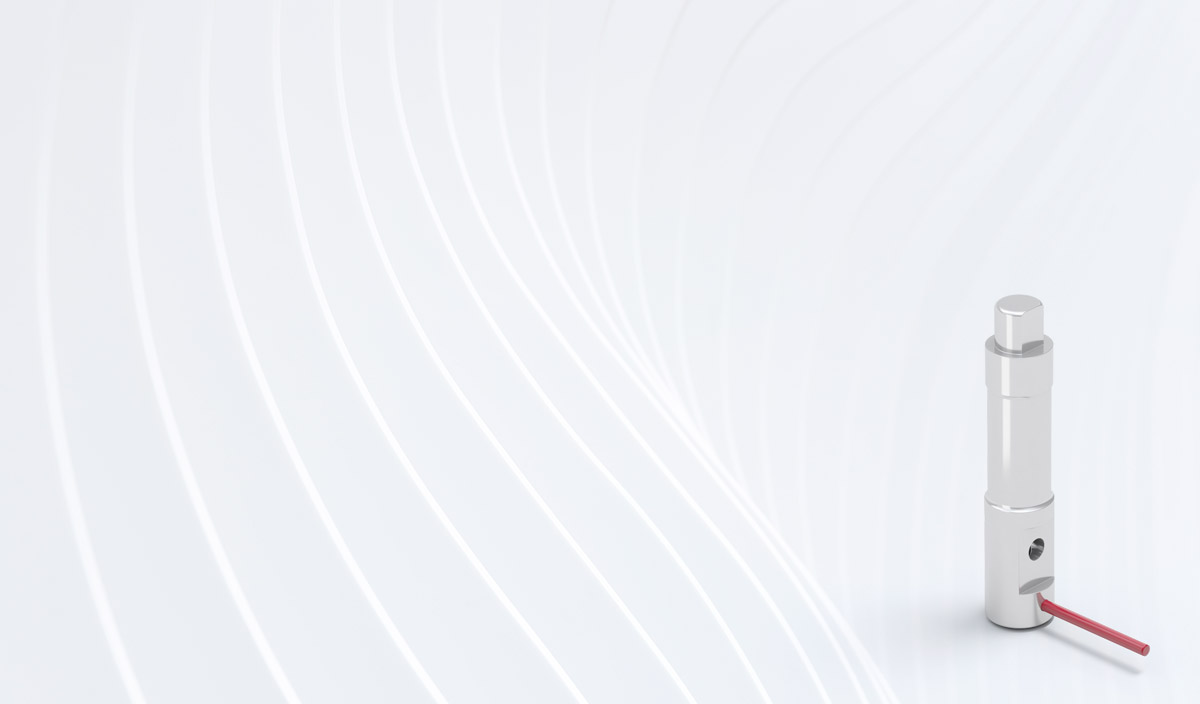
The smallest reaction torque sensor in our catalog
Description
Custom Miniature Reaction Torque Sensor for OEM. Custom miniature sensors.
Product Highlights And Features
The QTA136 reaction torque sensor is a state-of-the-art miniature sensor whose compact size opens up unprecedented possibilities. Its uniquely small footprint makes torque measurements possible in applications that don’t have enough space for a traditional torque sensor. The unit’s ultra-small 0.48in (12.2mm) diameter allows it to be tightly installed in applications with multiple motor drives. The sensor is built for OEM applications and has no outer casing, which further optimizes space utilization.
Compact footprint
The super small size of the 12.2mm diameter places it as the smallest in the FUTEK reaction torque portfolio. It is especially useful for applications with an array of motor drives, as it allows you to position the sensors in close proximity to one another. There are no mounting features, the unit is designed to be clamped in place, as most standard clamps can easily withstand torque levels above and beyond the sensing limits of the unit.
Custom-built for accuracy
QTA136 has a custom-built design with high-precision machining of the components that allows for accurate reading and reliability. The unit has an 18V input and 1.7mV/V output rating and can withstand temperatures up to 159.8°F (71°C) with high accuracy. The non-linearity is 0.2% and the non-repeatability is 0.1%.
Silicone cable
A standard 4-conductor cable allows voltage input and feedback output to external electronics for readout and control. The cable is spiral wound design with silicone grade material.
Low power consumption
With a 1000 Ohm bridge resistance, the QTA136 consumes significantly less current than a traditional sensor. This is especially valuable for any applications that are battery operated or are embedded in tight spaces where heat generation could become an issue.
Best in class material
The QTA136 is made of aircraft grade aluminum alloy grade AL2024-T4, a material that is known for its high stiffness and strength, allowing for a high natural frequency response that results in low deflection, minimizing fatigue, and ensuring high accuracy while measuring dynamic torque.
Wide applications
The QTA136 is particularly beneficial for robotic surgery applications as the sensor enhances assessment of anatomical structures and improved tissue characterization and manipulation. It is also well suited for dental drills, precision machining and assembly operations, directional control units in cube satellites, machining of composites, rheometers in pharma and chemical plants, microinjection molding force feedback units, prosthetic controls, as well as drones and UAVs.
Made in California
Designed and manufactured in-house. Our multidisciplinary engineering teams, high precision machining center, state-of-the-art quality assurance systems, and R&D and manufacturing facilities are all under one roof, allowing us to continuously reinvent and refine our products and processes.
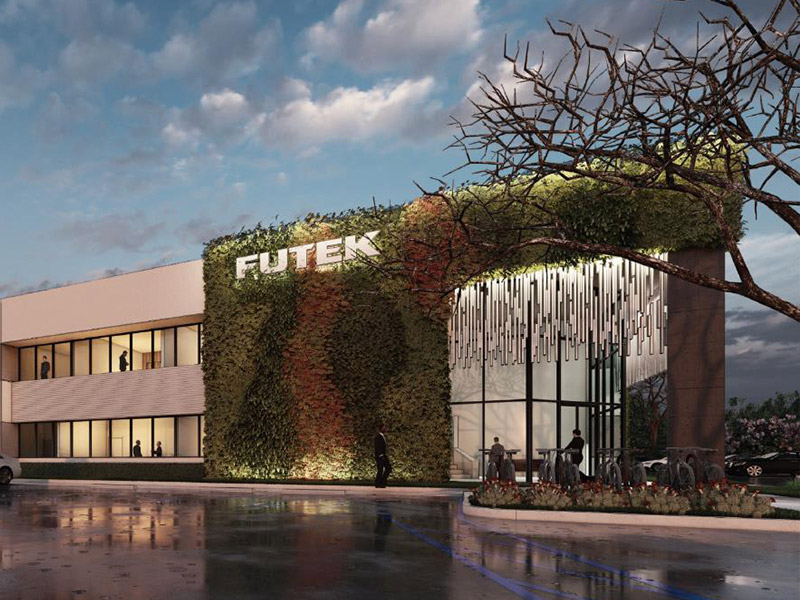
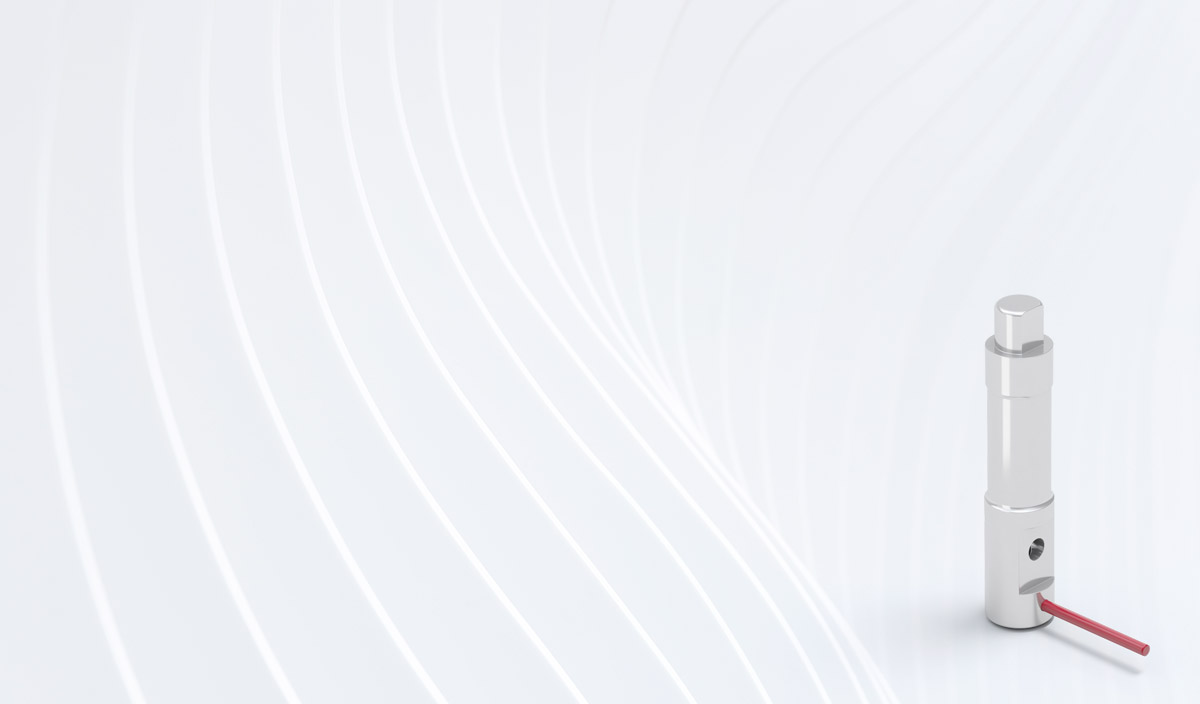
The smallest reaction torque sensor in our catalog
Description
Custom Miniature Reaction Torque Sensor for OEM. Custom miniature sensors.
Product Highlights And Features
The QTA136 reaction torque sensor is a state-of-the-art miniature sensor whose compact size opens up unprecedented possibilities. Its uniquely small footprint makes torque measurements possible in applications that don’t have enough space for a traditional torque sensor. The unit’s ultra-small 0.48in (12.2mm) diameter allows it to be tightly installed in applications with multiple motor drives. The sensor is built for OEM applications and has no outer casing, which further optimizes space utilization.
Compact footprint
The super small size of the 12.2mm diameter places it as the smallest in the FUTEK reaction torque portfolio. It is especially useful for applications with an array of motor drives, as it allows you to position the sensors in close proximity to one another. There are no mounting features, the unit is designed to be clamped in place, as most standard clamps can easily withstand torque levels above and beyond the sensing limits of the unit.
Custom-built for accuracy
QTA136 has a custom-built design with high-precision machining of the components that allows for accurate reading and reliability. The unit has an 18V input and 1.7mV/V output rating and can withstand temperatures up to 159.8°F (71°C) with high accuracy. The non-linearity is 0.2% and the non-repeatability is 0.1%.
Silicone cable
A standard 4-conductor cable allows voltage input and feedback output to external electronics for readout and control. The cable is spiral wound design with silicone grade material.
Low power consumption
With a 1000 Ohm bridge resistance, the QTA136 consumes significantly less current than a traditional sensor. This is especially valuable for any applications that are battery operated or are embedded in tight spaces where heat generation could become an issue.
Best in class material
The QTA136 is made of aircraft grade aluminum alloy grade AL2024-T4, a material that is known for its high stiffness and strength, allowing for a high natural frequency response that results in low deflection, minimizing fatigue, and ensuring high accuracy while measuring dynamic torque.
Wide applications
The QTA136 is particularly beneficial for robotic surgery applications as the sensor enhances assessment of anatomical structures and improved tissue characterization and manipulation. It is also well suited for dental drills, precision machining and assembly operations, directional control units in cube satellites, machining of composites, rheometers in pharma and chemical plants, microinjection molding force feedback units, prosthetic controls, as well as drones and UAVs.
Made in California
Designed and manufactured in-house. Our multidisciplinary engineering teams, high precision machining center, state-of-the-art quality assurance systems, and R&D and manufacturing facilities are all under one roof, allowing us to continuously reinvent and refine our products and processes.
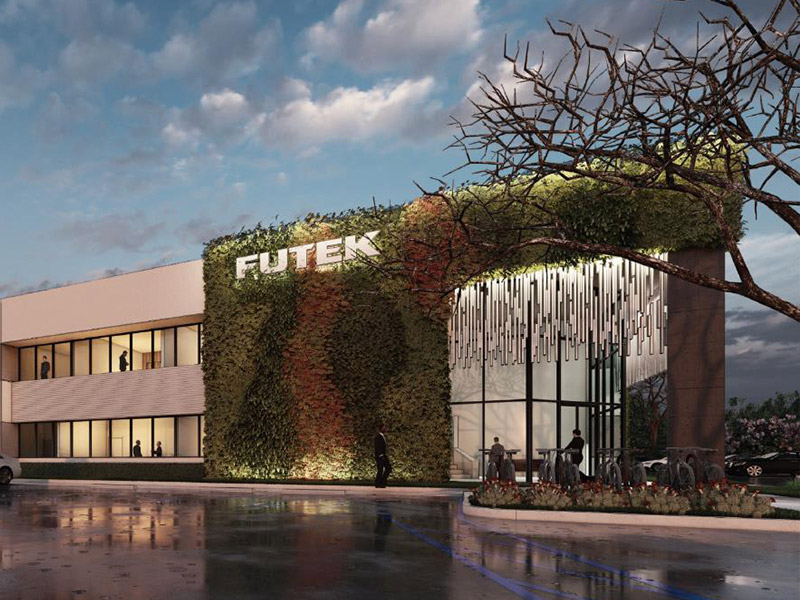