Micro Reaction Torque Sensor
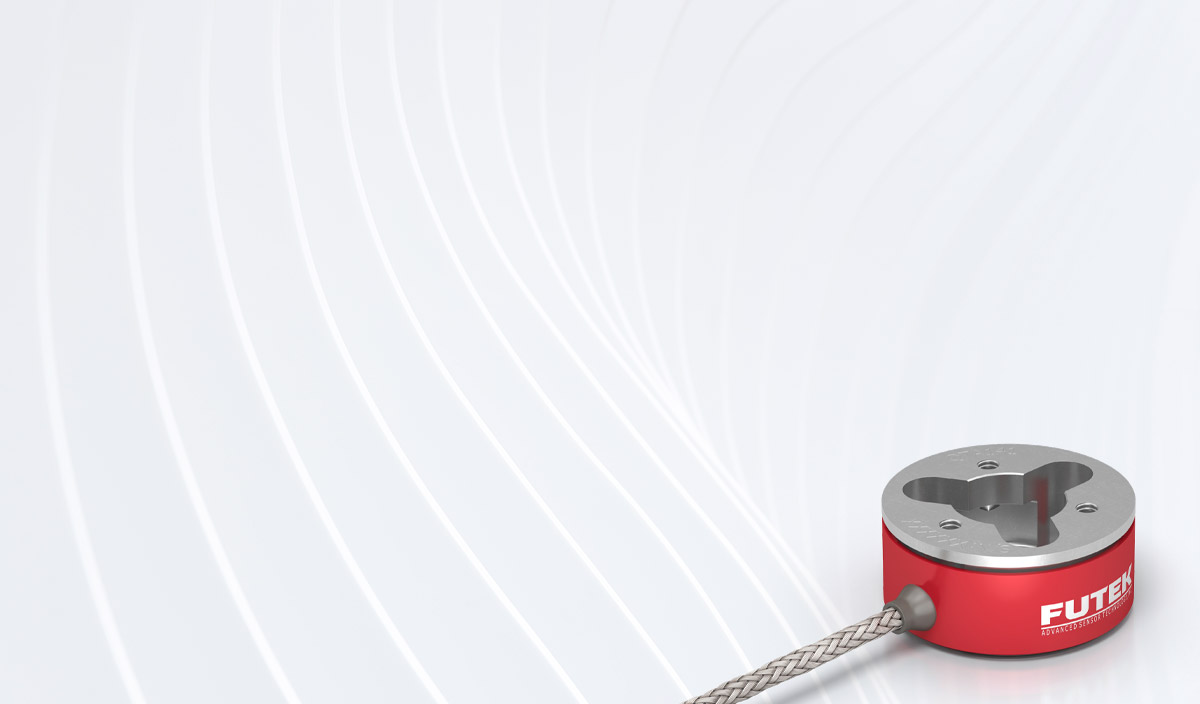
Minuscule size with state-of-the art precision
Description
The QTA141 micro reaction torque sensor is one of the smallest torque sensor in FUTEK’s catalog.
Its unique geometry allows it to fit in applications where precision closed-loop torque measurements have previously not been possible. By matching the motor/gearhead assembly diameter without adding to its size, the QTA141 allows for precise torque measurement in a very dense array, which maximizes the real state utilization of the assembly. Its unique motor mounting provisions do not require adapters, which would increase the system's height and weight.
- Allows for multiple mounting configurations
- Can mount directly onto a brushless DC motor
- A large ID supports the motor shaft coupler
- Very thin and flexible cable withstands the tight bending radius and physical stress associated with moving applications
- Can be integrated with electronics for custom requirements
- High precision and reliability
- Ideal for medical surgical robots or any dynamic application
- It can be modified to suit OEM applications
- Low height (10mm) allows easy integration to most joints and motor
Product Highlights And Features
- 5 times smaller than conventional torque sensors
- 10 times more accurate that current loop torque measurement
- Sized to mount to precision servo motors
The QTA141 micro reaction torque sensor is the smallest torque sensor in FUTEK's catalog. Its unique geometry allows it to fit in applications where precision closed-loop torque measurements have previously not been possible. It allows for multiple mounting configurations and can be integrated with electronics for custom requirements. By matching the motor/gearhead assembly diameter without adding to its size, the QTA141 allows for precise torque measurement in a very dense array, which maximizes the real state utilization of the assembly. Its unique motor mounting provisions do not require adapters, which would increase the system's height and weight. It’s especially well-suited for the fast-growing market of medical surgical robots, but offers excellent performance for any dynamic application. This model can also be modified to suit OEM applications. FUTEK offers application and engineering resources during DFM/DFX stage upon request.
Small and lightweight
The super small size of the QTA141 sensor at 0.86in (22mm) dia and 0.39in (10mm) height allows integration into systems and devices where space is at a premium, such as MedTech applications. At about 9g in weight, these sensors are also ideal for drones and even cube satellites.
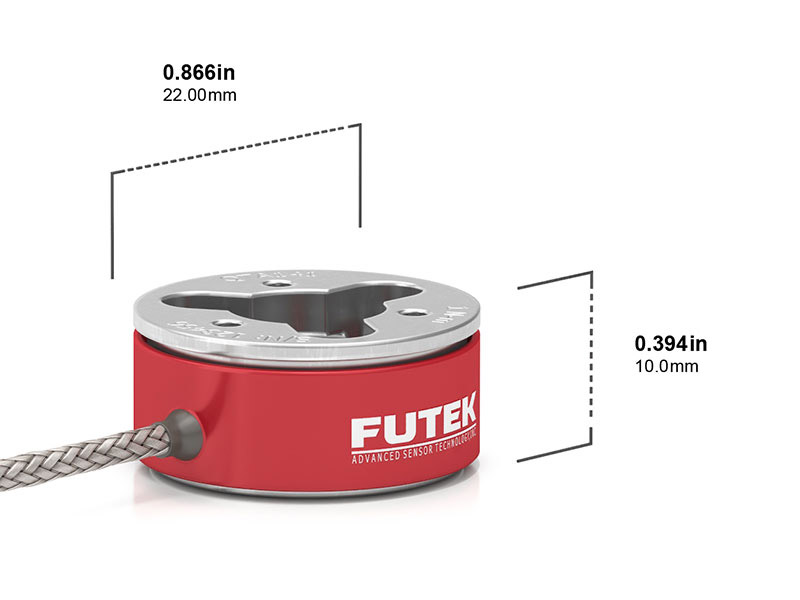
Dynamic measurement and control
The sensor can be mounted directly onto a brushless DC motor. The motor power can be controlled based on the torque feedback, providing dynamic feedback and precise control of the power that is used. In surgical applications, this can drastically reduce suture breakage.
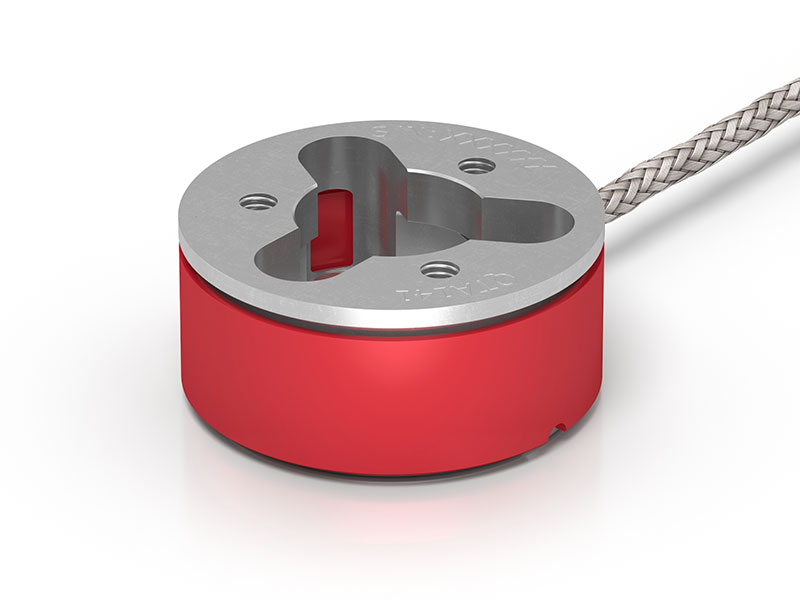
Mounting provisions
When mounting the QTA141 to a brushless DC motor, it needs to be installed with the motor shaft passing through the sensor’s through-hole without touching its inner diameter to avoid the indirect forces from the motor influencing the sensor’s measurements. To achieve this, a coupler can be used to extend the shaft and allow it to pass freely through the sensor.
Made to be accurate
A resistive circuit that converts torque input into a differential voltage output is the basic technology used in the sensor. Characteristics such as linearity, hysteresis, creep, stability, output shift over a temperature range, and off-axis load compensation are all taken care of in the design of this miniature sensor, guaranteeing high precision and reliability. Two models are available, one with 350 Ohm resistance and the other with 1000 Ohm resistance, covering torque ranges up to 1Nm and 2Nm respectively. The connector cable is of grade #34AWG, a 4-conductor cable with a braided cover that is 15cm long.
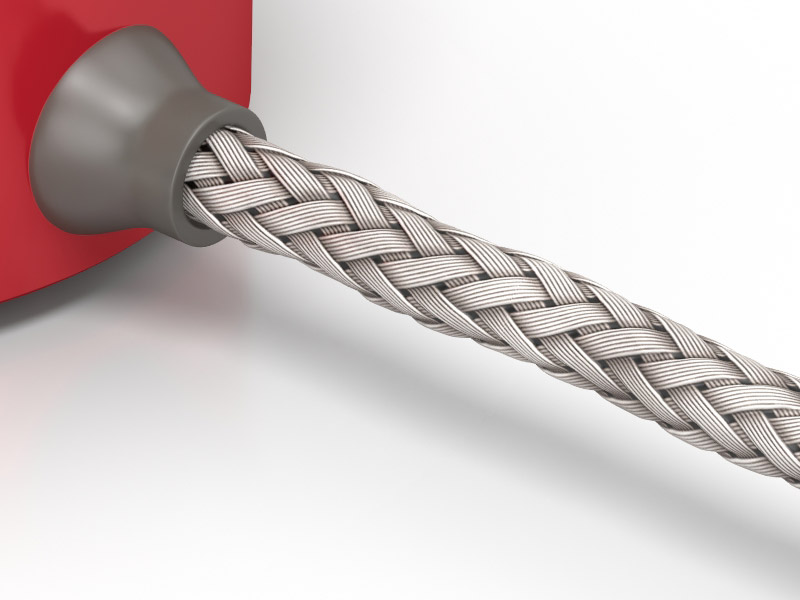
Ideal for medical robotics
The high-precision feedback offered by the QTA141 allows precise control of instruments in robotic surgery, providing fast response time and instant adaptation to torque variations. The low height of 10mm allows easy integration of the sensor to most joints and motors, providing a high degree of design flexibility and even late-stage addition to instruments. These sensors help enhance robotic platform dexterity, a key parameter for robotic learning. Specifically in robotic surgeries, the sensor enhances assessment of anatomical structures and improved tissue characterization and manipulation.
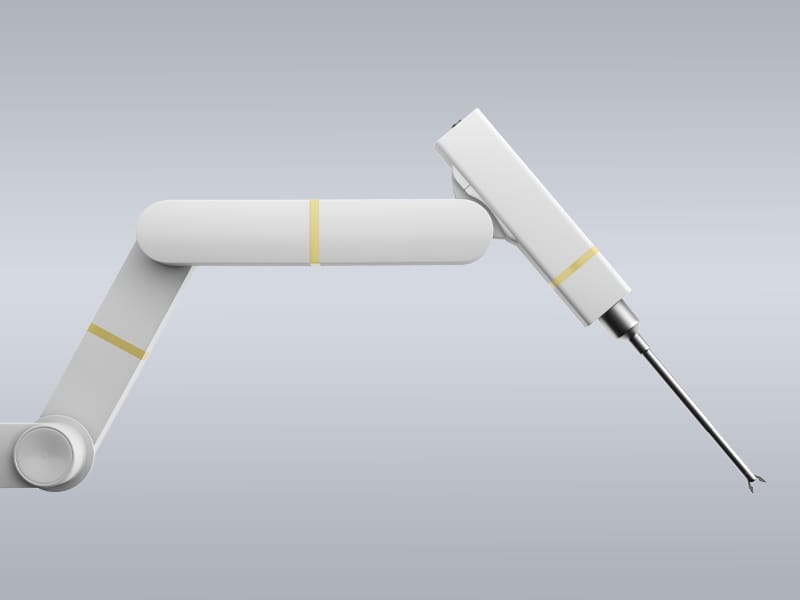
Wide applications
Miniature stationary and dynamic torque sensors find applications in surgical robots, dental drills, precision machining and assembly operations, directional control units in cube satellites, machining of composites, rheometers in pharma and chemical plants, microinjection molding force feedback units, prosthetic controls, as well as drones and UAVs.
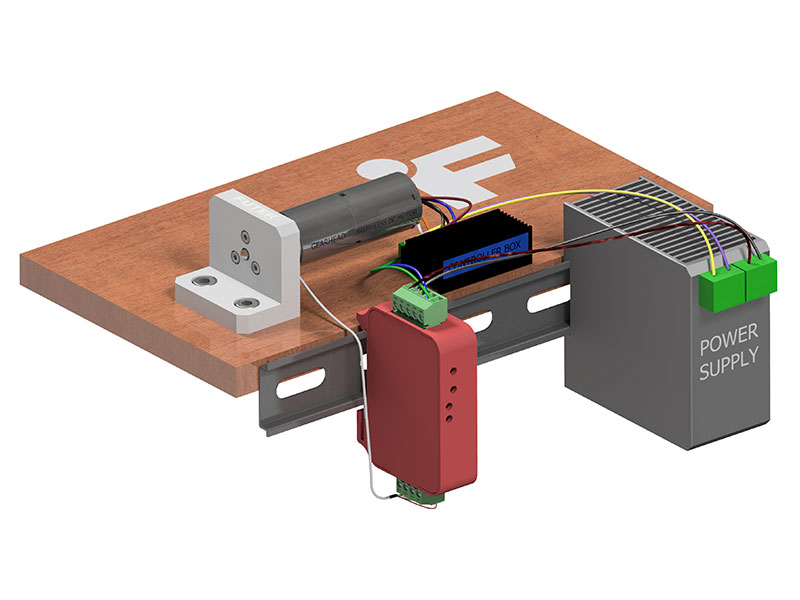
Made in Irvine, CA
Designed and manufactured in-house. Our multidisciplinary engineering teams, high precision machining center, state-of-the-art quality assurance systems, and R&D and manufacturing facilities are all under one roof, allowing us to continuously reinvent and refine our products and processes.
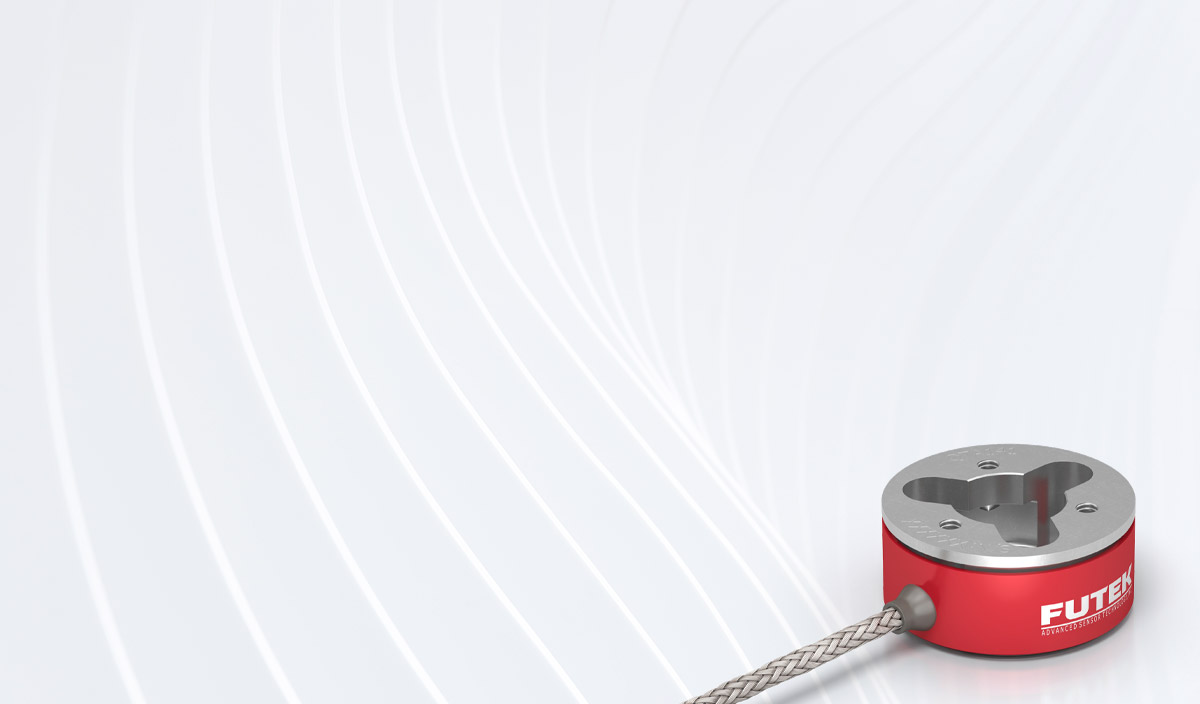
Minuscule size with state-of-the art precision
Description
The QTA141 micro reaction torque sensor is one of the smallest torque sensor in FUTEK’s catalog.
Its unique geometry allows it to fit in applications where precision closed-loop torque measurements have previously not been possible. By matching the motor/gearhead assembly diameter without adding to its size, the QTA141 allows for precise torque measurement in a very dense array, which maximizes the real state utilization of the assembly. Its unique motor mounting provisions do not require adapters, which would increase the system's height and weight.
- Allows for multiple mounting configurations
- Can mount directly onto a brushless DC motor
- A large ID supports the motor shaft coupler
- Very thin and flexible cable withstands the tight bending radius and physical stress associated with moving applications
- Can be integrated with electronics for custom requirements
- High precision and reliability
- Ideal for medical surgical robots or any dynamic application
- It can be modified to suit OEM applications
- Low height (10mm) allows easy integration to most joints and motor
Product Highlights And Features
- 5 times smaller than conventional torque sensors
- 10 times more accurate that current loop torque measurement
- Sized to mount to precision servo motors
The QTA141 micro reaction torque sensor is the smallest torque sensor in FUTEK's catalog. Its unique geometry allows it to fit in applications where precision closed-loop torque measurements have previously not been possible. It allows for multiple mounting configurations and can be integrated with electronics for custom requirements. By matching the motor/gearhead assembly diameter without adding to its size, the QTA141 allows for precise torque measurement in a very dense array, which maximizes the real state utilization of the assembly. Its unique motor mounting provisions do not require adapters, which would increase the system's height and weight. It’s especially well-suited for the fast-growing market of medical surgical robots, but offers excellent performance for any dynamic application. This model can also be modified to suit OEM applications. FUTEK offers application and engineering resources during DFM/DFX stage upon request.
Small and lightweight
The super small size of the QTA141 sensor at 0.86in (22mm) dia and 0.39in (10mm) height allows integration into systems and devices where space is at a premium, such as MedTech applications. At about 9g in weight, these sensors are also ideal for drones and even cube satellites.
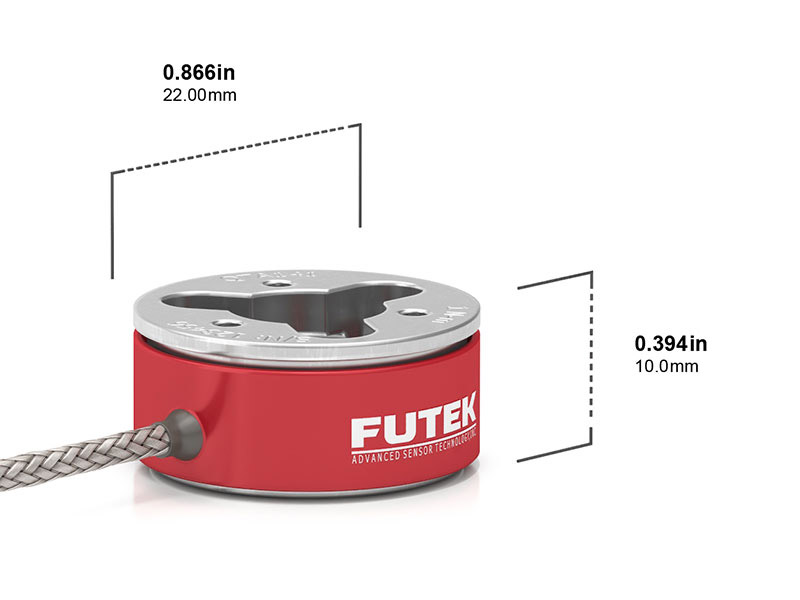
Dynamic measurement and control
The sensor can be mounted directly onto a brushless DC motor. The motor power can be controlled based on the torque feedback, providing dynamic feedback and precise control of the power that is used. In surgical applications, this can drastically reduce suture breakage.
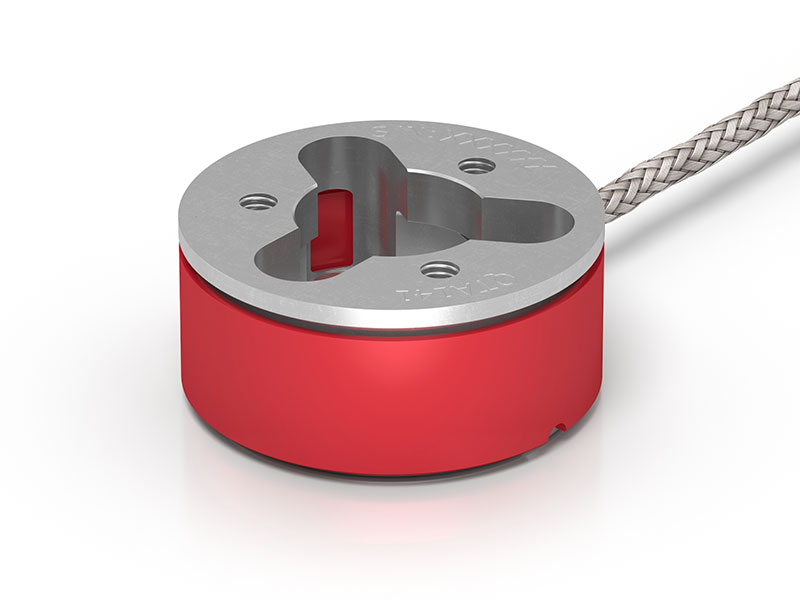
Mounting provisions
When mounting the QTA141 to a brushless DC motor, it needs to be installed with the motor shaft passing through the sensor’s through-hole without touching its inner diameter to avoid the indirect forces from the motor influencing the sensor’s measurements. To achieve this, a coupler can be used to extend the shaft and allow it to pass freely through the sensor.
Made to be accurate
A resistive circuit that converts torque input into a differential voltage output is the basic technology used in the sensor. Characteristics such as linearity, hysteresis, creep, stability, output shift over a temperature range, and off-axis load compensation are all taken care of in the design of this miniature sensor, guaranteeing high precision and reliability. Two models are available, one with 350 Ohm resistance and the other with 1000 Ohm resistance, covering torque ranges up to 1Nm and 2Nm respectively. The connector cable is of grade #34AWG, a 4-conductor cable with a braided cover that is 15cm long.
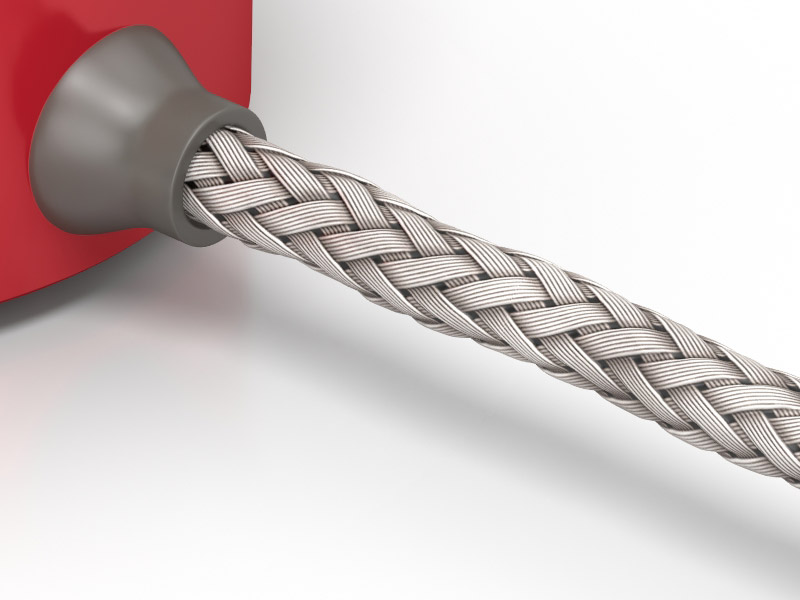
Ideal for medical robotics
The high-precision feedback offered by the QTA141 allows precise control of instruments in robotic surgery, providing fast response time and instant adaptation to torque variations. The low height of 10mm allows easy integration of the sensor to most joints and motors, providing a high degree of design flexibility and even late-stage addition to instruments. These sensors help enhance robotic platform dexterity, a key parameter for robotic learning. Specifically in robotic surgeries, the sensor enhances assessment of anatomical structures and improved tissue characterization and manipulation.
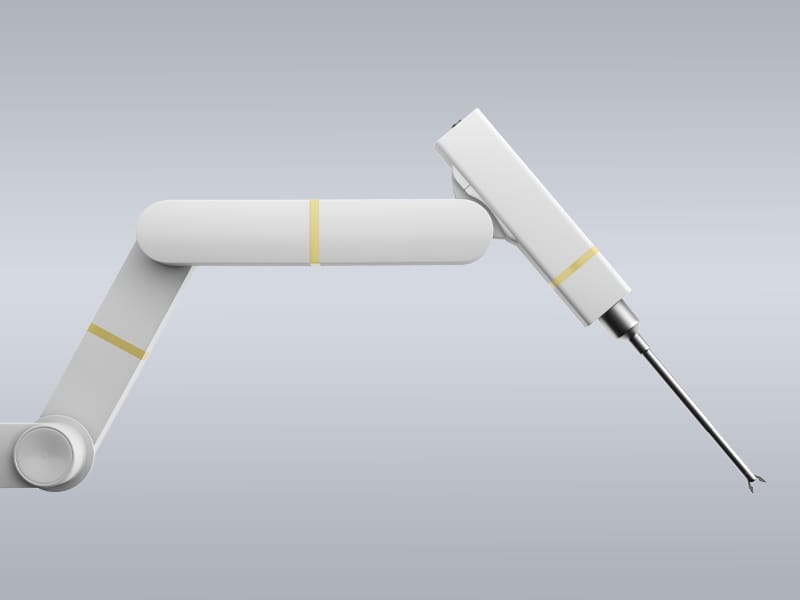
Wide applications
Miniature stationary and dynamic torque sensors find applications in surgical robots, dental drills, precision machining and assembly operations, directional control units in cube satellites, machining of composites, rheometers in pharma and chemical plants, microinjection molding force feedback units, prosthetic controls, as well as drones and UAVs.
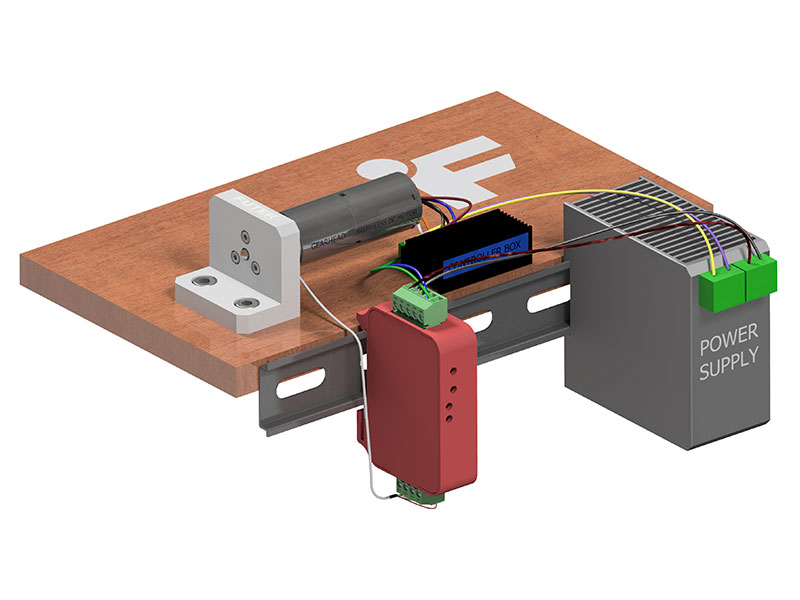
Made in Irvine, CA
Designed and manufactured in-house. Our multidisciplinary engineering teams, high precision machining center, state-of-the-art quality assurance systems, and R&D and manufacturing facilities are all under one roof, allowing us to continuously reinvent and refine our products and processes.