Subminiature Load Button
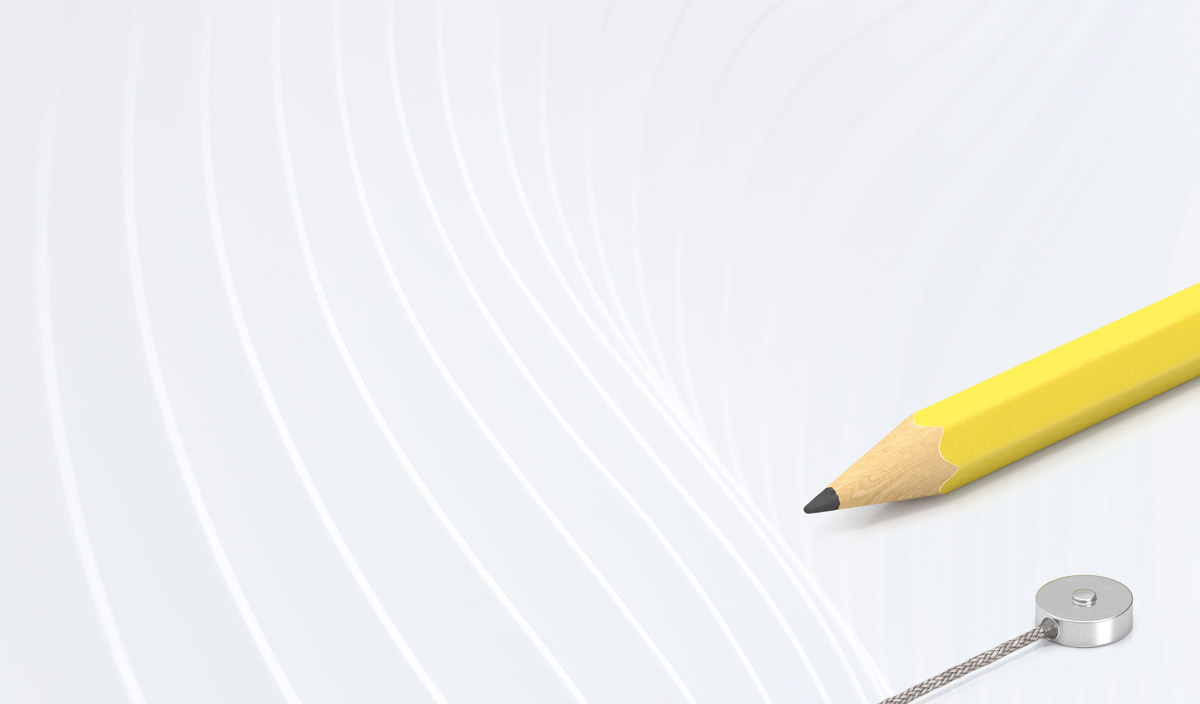
Extremely accurate with a miniscule footprint
Description
Model LLB130 is a Miniature Load Button designed for Press, or Inline compression applications. The LLB130 Mini Force Sensor is made from a robust 17-4 PH Stainless Steel, with a subminiature 0.38 inch outside diameter. These subminiature load cells achieve great accuracy and stiffness with a Nonlinearity of ±0.5% and Deflection of 0.002” nominal. You will also find sub miniature load cells for external matched output readily available.
The standard LLB130 Subminiature Load Cell (aka sub-miniature load cell) can be modified or customized to meet your requirements and most capacities are in our inventory, making them available for quick delivery.
Force Sensor Features:
- Fully internally temperature compensated (no external conditioning circuitry)
- Sub-miniature load cell / lightweight
- Low deflection / fast response
- 17-4 PH stainless steel construction
- For use in compression
- Utilizes metal foil strain gauge technology
- Adheres to RoHS directive 2015/863/EU
- Accessories and related signal conditioners and amplifiers available
If you are looking for a Shear Beam Load cell, check out our LSB201 S Beam Miniature Load Cell.
Product Highlights And Features
- Fully internally temperature compensated (no external conditioning circuitry)
- Sub-miniature load cell / light weight
- Low deflection / fast response
- 17-4 PH stainless-steel construction
- For use in compression
- Utilizes metal foil strain gauge technology
- Adheres to RoHS directive 2015/863/EU
- Accessories and related instruments available
LLB130 is a subminiature load button with extraordinarily high accuracy and reliability. Measuring compression with a tiny footprint of a 0.38in (9.5mm) outside diameter and 0.13in (3.3 mm) height, the LLB130 features a custom single-gauge design for robust integration with the sensor case that completely eliminates inter-gauge wiring, leading to enhanced calibration performance. A customized strain element allows increased strain measurement around the active sensor element that reduces reproducibility errors and installation mishaps.
The LLB130 offers a capacity range from as low as 35.27 oz (1000g) up to 50lb (22.68kg). The diverse and durable sensor is designed for press or inline compression applications, such as measuring loads on a turbine shaft or gauging forces on a CNC workpiece. The sensor has a highly flexible 34 AWG, 4-conductor, 5-foot (1.5 m) long braided shielded cable. This model can also be modified to suit OEM applications. FUTEK offers application and engineering resources during DFM/DFX stage upon request.
Range and flexibility
LLB130 series offers load buttons that measure compressive loads from as low as 35.27oz (1000g) up to 50lb (22.68kg). Its highly flexible mounting options include securement from the outer lip, retention with screws, or mounting inside a counterbore hole.
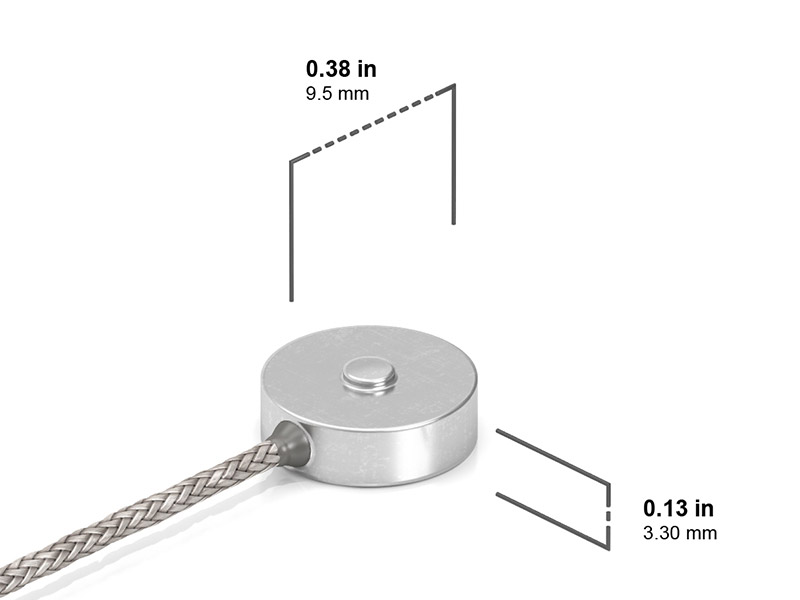
Designed for precision
The spherical radius of the load button has been designed to maintain the highest possible level of accuracy. By minimizing contact with the loading provisions, the button’s spherical shape transfers the load evenly over the sensing area, compensating for potential misalignments.
Powerful performance
The LLB130 delivers a remarkably high natural frequency (starting at 20kHz and going up to 52 kHz) which provides a fast response time that benefits accuracy and cycle time reduction. The precision of the sensor is also augmented by its high stiffness, which leads to a very low deflection of 0.0005in (0.013mm).
Moisture resistant
With an IP64 rating, the product is dustproof and can withstand splashing water from any direction. This opens up more options for applications as it will allow usage in highly humid conditions.
Reducing error
A highly customized strain element has been designed to allow more strain measurement around the active sensor element, which reduces reproducibility errors from off-axis loads. It also makes the sensor less sensitive to installation mishaps.
Interior thermal compensation
The LLB130 features a monolithic sensing element with integrated zero balance and thermal compensation, which reduces the risk of accidentally removing compensation circuitry.
Flexible cable
The sensor cable is a highly flexible 34 AWG, 4-conductor, 5-foot (1.5m) long braided shielded cable that bends easily within a very tight radius. A braided shield physically covers the signal wires while significantly reducing interference from stray magnetic and static electric fields. Although extremely flexible, the cable is not intended for high flex cycles.
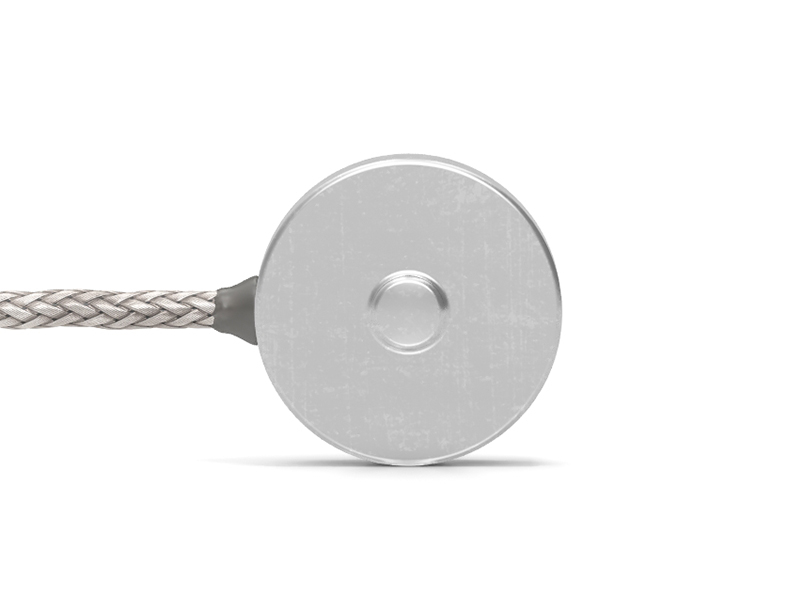
Robust construction
The stainless steel body provides outstanding strength and corrosion resistance and provides enhanced protection against physical damage in addition to withstanding other harsh environmental conditions. A special heat treatment process has been applied to the flexure to improve durability, extending the life-cycle of the sensor. Additionally, the metallic load cell housing significantly reduces interference and unwanted environmental conditions that would affect the accuracy and reliability.
Best-in-class material
The exceptional quality of this sensor makes it highly durable and reliable. Its body is made of aerospace-grade 17-4 precipitation hardened stainless steel, which provides high strength, high hardness, and corrosion resistance over a wide temperature range.
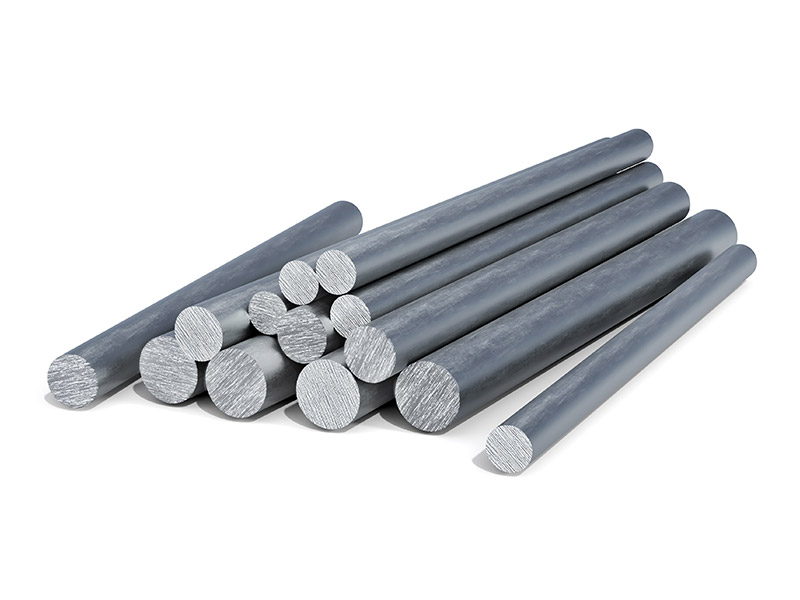
Calibration included
The LLB130 has been tested by FUTEK’s world-class calibration department and is NIST traceable. We can also reduce hidden costs and setup time by calibrating your sensor with FUTEK electronics of your choice. In addition, we offer calibration to ANSI Z540-1 and ISO 17025 standards upon request.
Made in Irvine, CA
Designed and manufactured in-house. Our multidisciplinary engineering teams, high precision machining center, state-of-the-art quality assurance systems, and R&D and manufacturing facilities are all under one roof, allowing us to continuously reinvent and refine our products and processes.
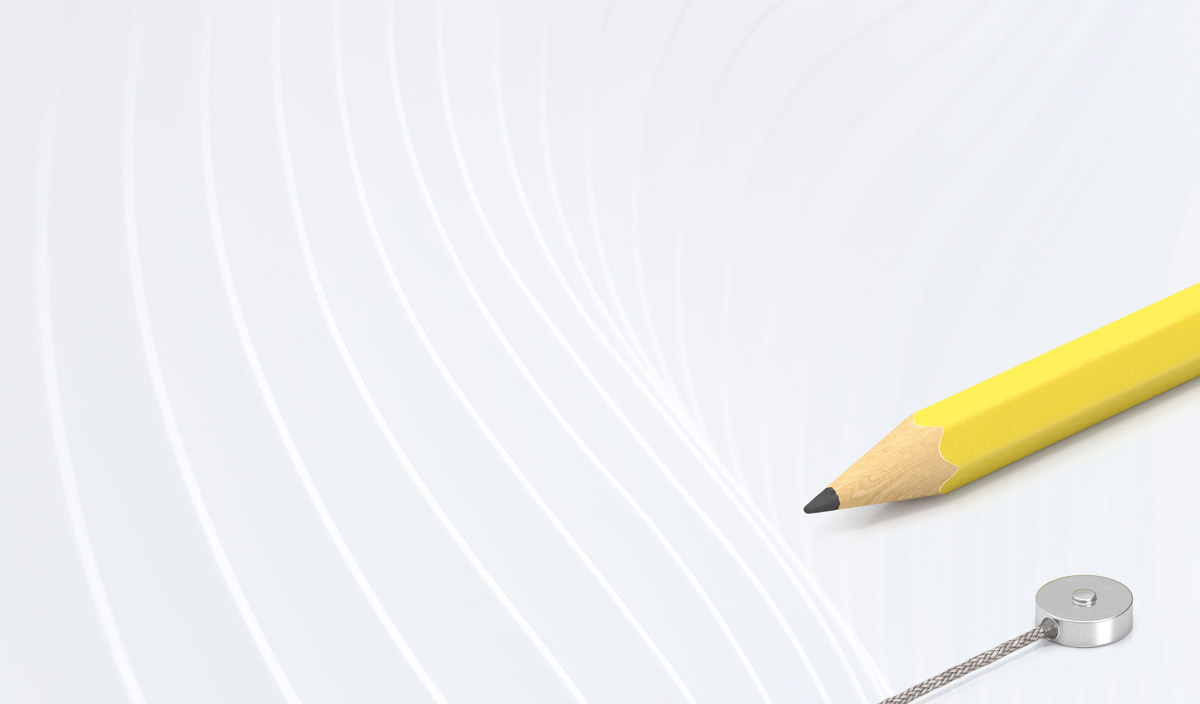
Extremely accurate with a miniscule footprint
Description
Model LLB130 is a Miniature Load Button designed for Press, or Inline compression applications. The LLB130 Mini Force Sensor is made from a robust 17-4 PH Stainless Steel, with a subminiature 0.38 inch outside diameter. These subminiature load cells achieve great accuracy and stiffness with a Nonlinearity of ±0.5% and Deflection of 0.002” nominal. You will also find sub miniature load cells for external matched output readily available.
The standard LLB130 Subminiature Load Cell (aka sub-miniature load cell) can be modified or customized to meet your requirements and most capacities are in our inventory, making them available for quick delivery.
Force Sensor Features:
- Fully internally temperature compensated (no external conditioning circuitry)
- Sub-miniature load cell / lightweight
- Low deflection / fast response
- 17-4 PH stainless steel construction
- For use in compression
- Utilizes metal foil strain gauge technology
- Adheres to RoHS directive 2015/863/EU
- Accessories and related signal conditioners and amplifiers available
If you are looking for a Shear Beam Load cell, check out our LSB201 S Beam Miniature Load Cell.
Product Highlights And Features
- Fully internally temperature compensated (no external conditioning circuitry)
- Sub-miniature load cell / light weight
- Low deflection / fast response
- 17-4 PH stainless-steel construction
- For use in compression
- Utilizes metal foil strain gauge technology
- Adheres to RoHS directive 2015/863/EU
- Accessories and related instruments available
LLB130 is a subminiature load button with extraordinarily high accuracy and reliability. Measuring compression with a tiny footprint of a 0.38in (9.5mm) outside diameter and 0.13in (3.3 mm) height, the LLB130 features a custom single-gauge design for robust integration with the sensor case that completely eliminates inter-gauge wiring, leading to enhanced calibration performance. A customized strain element allows increased strain measurement around the active sensor element that reduces reproducibility errors and installation mishaps.
The LLB130 offers a capacity range from as low as 35.27 oz (1000g) up to 50lb (22.68kg). The diverse and durable sensor is designed for press or inline compression applications, such as measuring loads on a turbine shaft or gauging forces on a CNC workpiece. The sensor has a highly flexible 34 AWG, 4-conductor, 5-foot (1.5 m) long braided shielded cable. This model can also be modified to suit OEM applications. FUTEK offers application and engineering resources during DFM/DFX stage upon request.
Range and flexibility
LLB130 series offers load buttons that measure compressive loads from as low as 35.27oz (1000g) up to 50lb (22.68kg). Its highly flexible mounting options include securement from the outer lip, retention with screws, or mounting inside a counterbore hole.
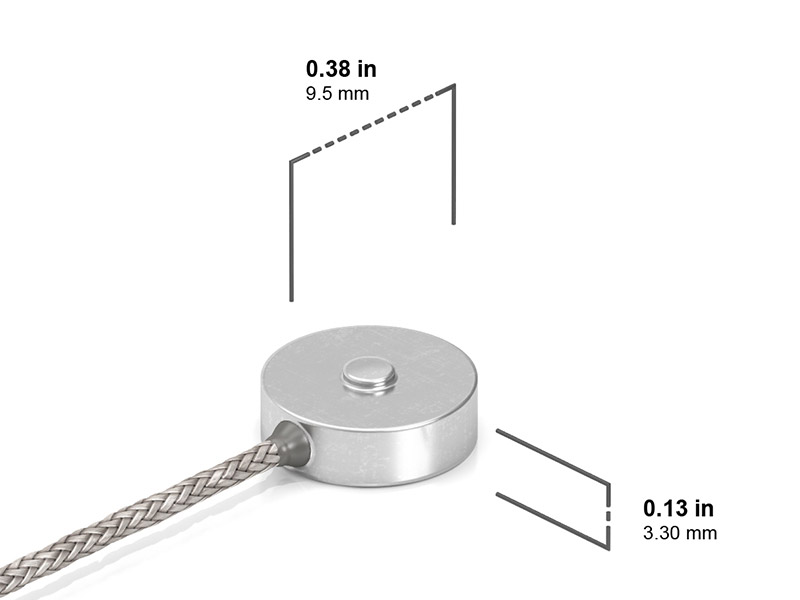
Designed for precision
The spherical radius of the load button has been designed to maintain the highest possible level of accuracy. By minimizing contact with the loading provisions, the button’s spherical shape transfers the load evenly over the sensing area, compensating for potential misalignments.
Powerful performance
The LLB130 delivers a remarkably high natural frequency (starting at 20kHz and going up to 52 kHz) which provides a fast response time that benefits accuracy and cycle time reduction. The precision of the sensor is also augmented by its high stiffness, which leads to a very low deflection of 0.0005in (0.013mm).
Moisture resistant
With an IP64 rating, the product is dustproof and can withstand splashing water from any direction. This opens up more options for applications as it will allow usage in highly humid conditions.
Reducing error
A highly customized strain element has been designed to allow more strain measurement around the active sensor element, which reduces reproducibility errors from off-axis loads. It also makes the sensor less sensitive to installation mishaps.
Interior thermal compensation
The LLB130 features a monolithic sensing element with integrated zero balance and thermal compensation, which reduces the risk of accidentally removing compensation circuitry.
Flexible cable
The sensor cable is a highly flexible 34 AWG, 4-conductor, 5-foot (1.5m) long braided shielded cable that bends easily within a very tight radius. A braided shield physically covers the signal wires while significantly reducing interference from stray magnetic and static electric fields. Although extremely flexible, the cable is not intended for high flex cycles.
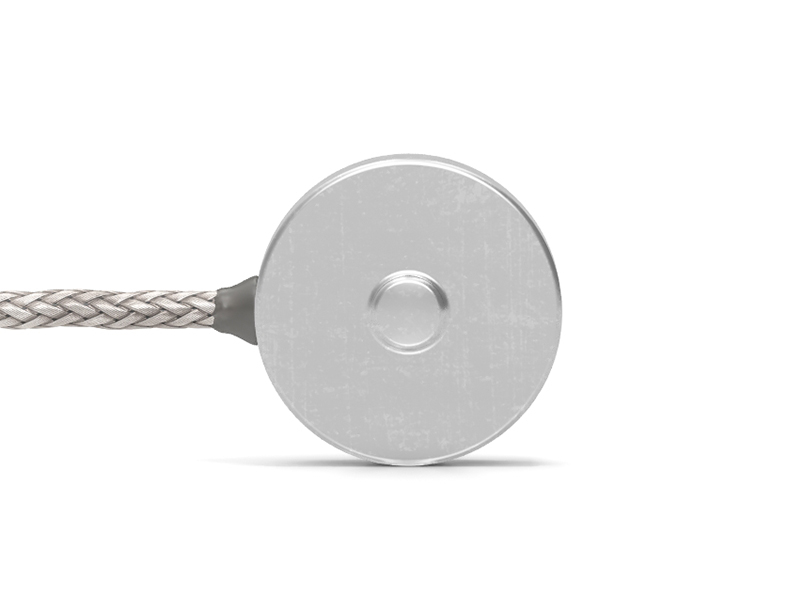
Robust construction
The stainless steel body provides outstanding strength and corrosion resistance and provides enhanced protection against physical damage in addition to withstanding other harsh environmental conditions. A special heat treatment process has been applied to the flexure to improve durability, extending the life-cycle of the sensor. Additionally, the metallic load cell housing significantly reduces interference and unwanted environmental conditions that would affect the accuracy and reliability.
Best-in-class material
The exceptional quality of this sensor makes it highly durable and reliable. Its body is made of aerospace-grade 17-4 precipitation hardened stainless steel, which provides high strength, high hardness, and corrosion resistance over a wide temperature range.
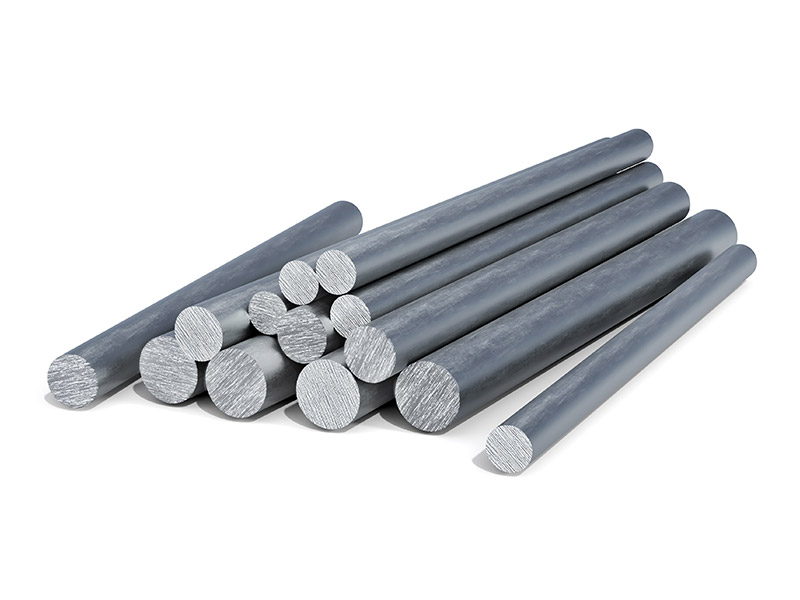
Calibration included
The LLB130 has been tested by FUTEK’s world-class calibration department and is NIST traceable. We can also reduce hidden costs and setup time by calibrating your sensor with FUTEK electronics of your choice. In addition, we offer calibration to ANSI Z540-1 and ISO 17025 standards upon request.
Made in Irvine, CA
Designed and manufactured in-house. Our multidisciplinary engineering teams, high precision machining center, state-of-the-art quality assurance systems, and R&D and manufacturing facilities are all under one roof, allowing us to continuously reinvent and refine our products and processes.