Miniature Load Button with Threaded/Tapped Holes
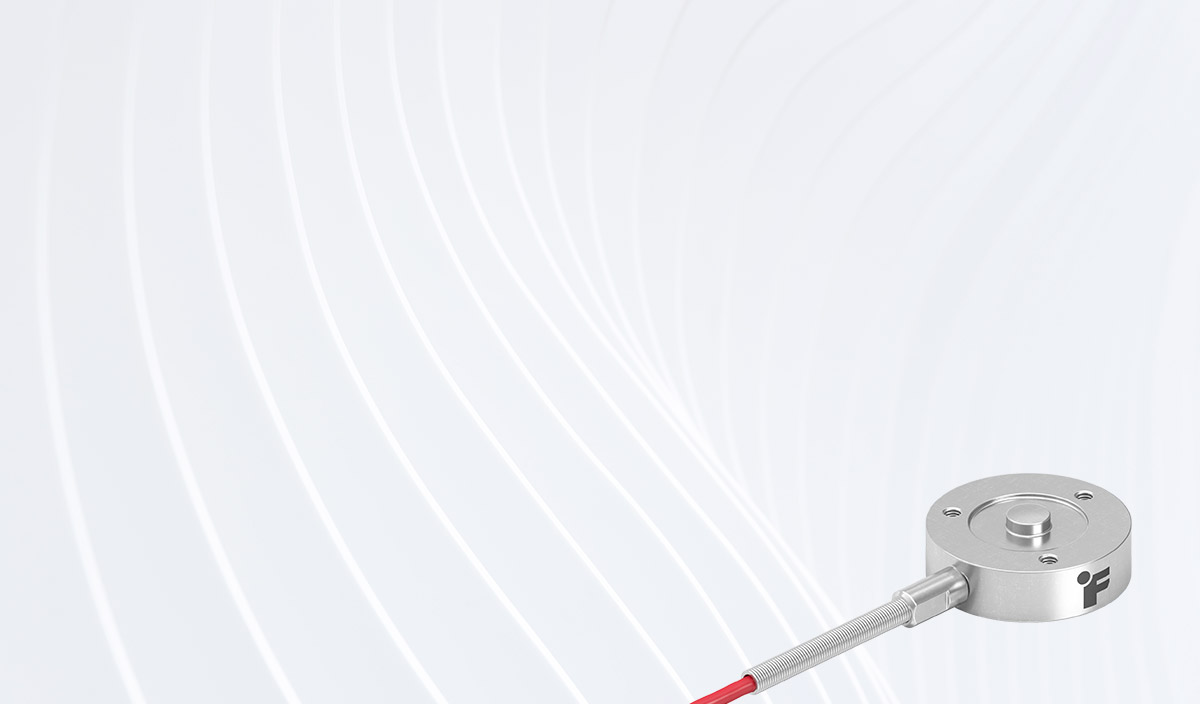
Compact and durable load button for press compression applications
Description
Model LLB350 is a Miniature Load Button with Threaded Mounting Holes built for Press, or Inline compression applications. The standard LLB350 Miniature Load Button model has a very robust construction available in 17-4 Stainless Steel, with a 1.0” outside diameter and a 10 feet long 29 AWG 4 conductor shielded Teflon cable. You will also find options for external matched output readily available.
The Miniature Load Button offers high accuracy. It has Nonlinearity of ±0.5% and Deflection of 0.003” nominal. The standard LLB350 Miniature Load Button can be modified or customized to meet your requirements and most capacities are in our inventory, making them available for 24-hour shipping.
Product Highlights And Features
- Ultra low deflection
- Robust strain relief
- 17-4 PH stainless-steel construction
- For use in compression
- Utilizes metal foil strain gauge technology
The unrivaled durability and accuracy of the miniature load button LLB350 has made it a very popular choice for press compression applications. The sensor has a compact form factor with a diameter of only 0.98in (24.9mm) and a height of only 0.32in (8.1mm), a capacity 25 to 50lb (11.34 to 22.6kg), and screw down mounting provisions for ease of fixturing and integration. LLB350 fuses an internally balanced and thermally compensated bridge with mechanical cable strain relief, creating the ultimate combination of performance and reliability. This model can also be modified to suit OEM applications. FUTEK offers application and engineering resources during DFM/DFX stage upon request.
Range and mounting
The LLB350 series offers load buttons in two capacity options that measure compressive loads from 25 to 50lb (11.34 to 22.6kg). Three threaded holes allows the part to be securely mounted from the bottom.
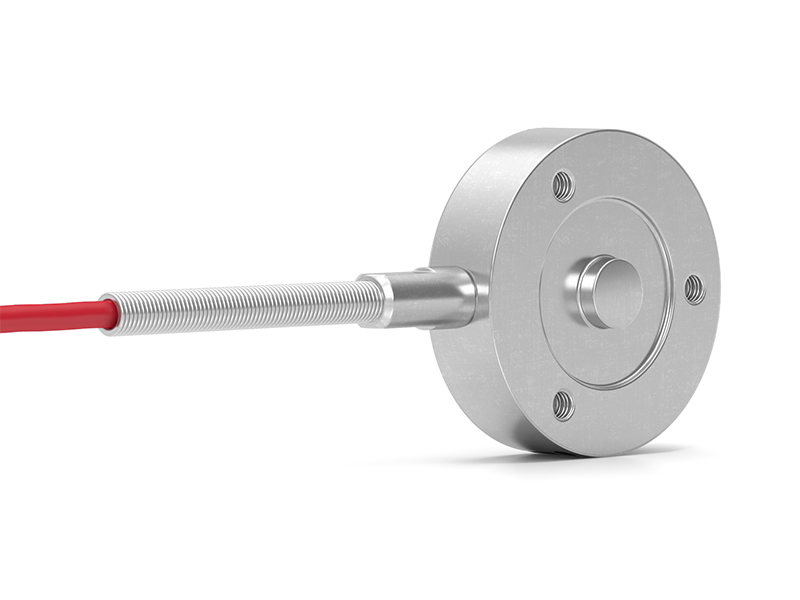
Robust construction
The sensor’s aerospace alloy stainless steel body provides not only outstanding creep and fatigue performance, but also corrosion resistance and enhanced protection against harsh environments. A special heat treatment process has been applied to the flexure to improve durability, extending the life-cycle of the sensor.
Best-in-class material
The exceptional quality of this sensor makes it highly durable and reliable. Its body is made of aerospace-grade 17-4 precipitation hardened stainless steel, which provides high strength, high hardness, and corrosion resistance over a wide temperature range.
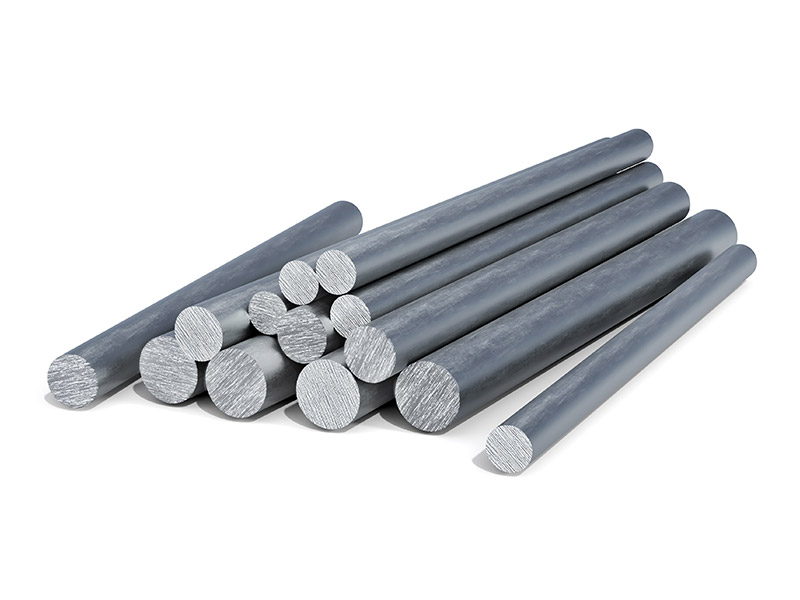
Made to be accurate
The LLB350 has a rated non-linearity and hysteresis of ±0.5% with 0.1% non-repeatability. Its precision is also augmented by its high stiffness, which leads to a very low deflection with some capacities as low as 0.0005in (0.0127mm).
Designed for precision
The spherical radius of the load button has been designed to maintain the highest possible level of accuracy. By minimizing contact with the loading provisions, the button’s spherical shape transfers the load evenly over the sensing area, compensating for potential misalignments.
Tough-as-nails cable
The sensor cable is a 29 AWG, 4-conductor, 10-foot (3m) long cable with spiral shielding and a Teflon outer jacket. It is a mechanically crimped cable with strain relief that enables a very high level of security for harsh environments where the cable undergoes thousands and thousands of bend-unbend cycles.
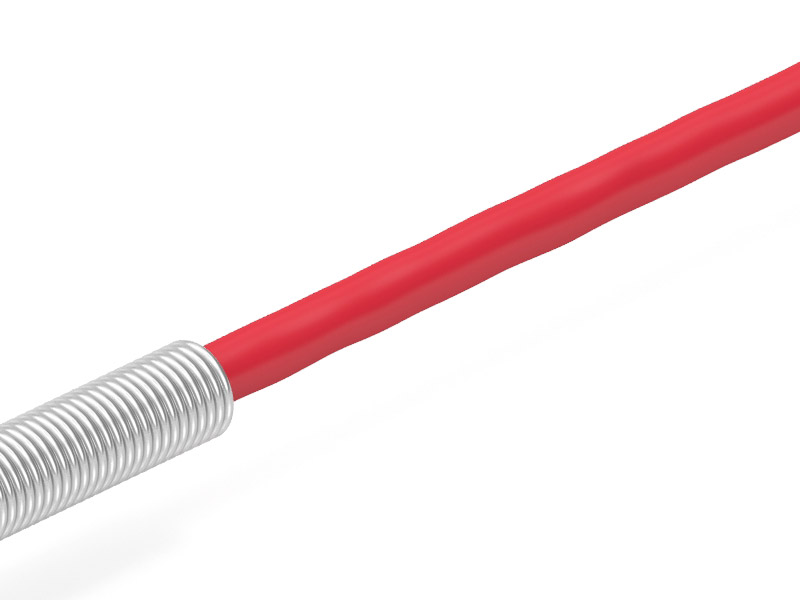
Calibration included
The LLB350 has been tested by FUTEK’s world-class calibration department and is NIST traceable. We can also reduce hidden costs and setup time by calibrating your sensor with FUTEK electronics of your choice. In addition, we offer calibration to ANSI Z540-1 and ISO 17025 standards upon request.
Made in Irvine, CA
Designed and manufactured in-house. Our multidisciplinary engineering teams, high precision machining center, state-of-the-art quality assurance systems, and R&D and manufacturing facilities are all under one roof, allowing us to continuously reinvent and refine our products and processes.
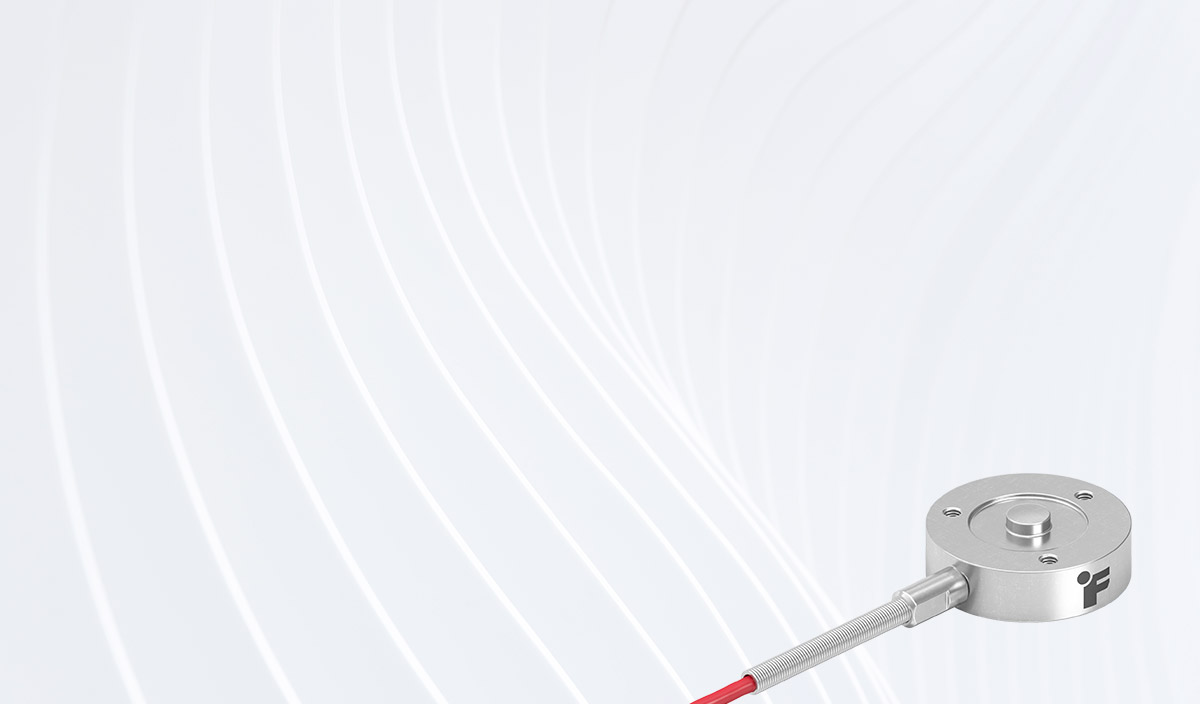
Compact and durable load button for press compression applications
Description
Model LLB350 is a Miniature Load Button with Threaded Mounting Holes built for Press, or Inline compression applications. The standard LLB350 Miniature Load Button model has a very robust construction available in 17-4 Stainless Steel, with a 1.0” outside diameter and a 10 feet long 29 AWG 4 conductor shielded Teflon cable. You will also find options for external matched output readily available.
The Miniature Load Button offers high accuracy. It has Nonlinearity of ±0.5% and Deflection of 0.003” nominal. The standard LLB350 Miniature Load Button can be modified or customized to meet your requirements and most capacities are in our inventory, making them available for 24-hour shipping.
Product Highlights And Features
- Ultra low deflection
- Robust strain relief
- 17-4 PH stainless-steel construction
- For use in compression
- Utilizes metal foil strain gauge technology
The unrivaled durability and accuracy of the miniature load button LLB350 has made it a very popular choice for press compression applications. The sensor has a compact form factor with a diameter of only 0.98in (24.9mm) and a height of only 0.32in (8.1mm), a capacity 25 to 50lb (11.34 to 22.6kg), and screw down mounting provisions for ease of fixturing and integration. LLB350 fuses an internally balanced and thermally compensated bridge with mechanical cable strain relief, creating the ultimate combination of performance and reliability. This model can also be modified to suit OEM applications. FUTEK offers application and engineering resources during DFM/DFX stage upon request.
Range and mounting
The LLB350 series offers load buttons in two capacity options that measure compressive loads from 25 to 50lb (11.34 to 22.6kg). Three threaded holes allows the part to be securely mounted from the bottom.
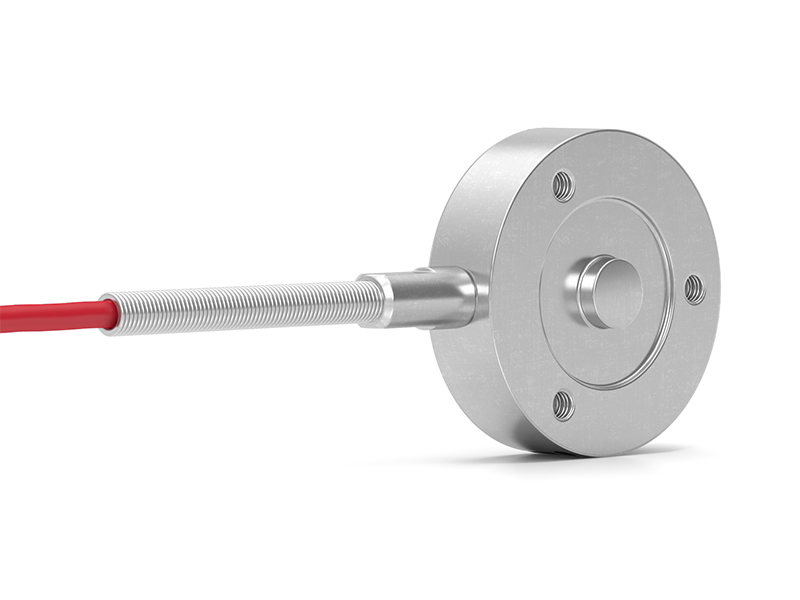
Robust construction
The sensor’s aerospace alloy stainless steel body provides not only outstanding creep and fatigue performance, but also corrosion resistance and enhanced protection against harsh environments. A special heat treatment process has been applied to the flexure to improve durability, extending the life-cycle of the sensor.
Best-in-class material
The exceptional quality of this sensor makes it highly durable and reliable. Its body is made of aerospace-grade 17-4 precipitation hardened stainless steel, which provides high strength, high hardness, and corrosion resistance over a wide temperature range.
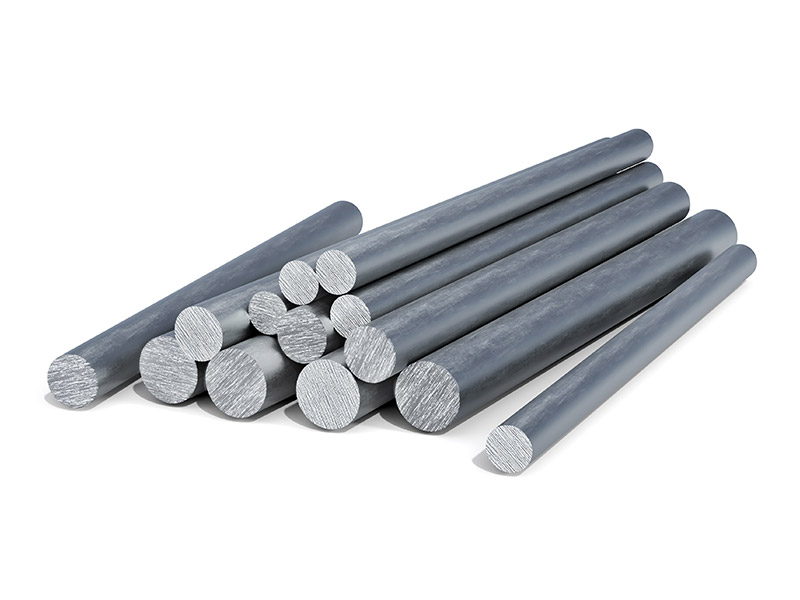
Made to be accurate
The LLB350 has a rated non-linearity and hysteresis of ±0.5% with 0.1% non-repeatability. Its precision is also augmented by its high stiffness, which leads to a very low deflection with some capacities as low as 0.0005in (0.0127mm).
Designed for precision
The spherical radius of the load button has been designed to maintain the highest possible level of accuracy. By minimizing contact with the loading provisions, the button’s spherical shape transfers the load evenly over the sensing area, compensating for potential misalignments.
Tough-as-nails cable
The sensor cable is a 29 AWG, 4-conductor, 10-foot (3m) long cable with spiral shielding and a Teflon outer jacket. It is a mechanically crimped cable with strain relief that enables a very high level of security for harsh environments where the cable undergoes thousands and thousands of bend-unbend cycles.
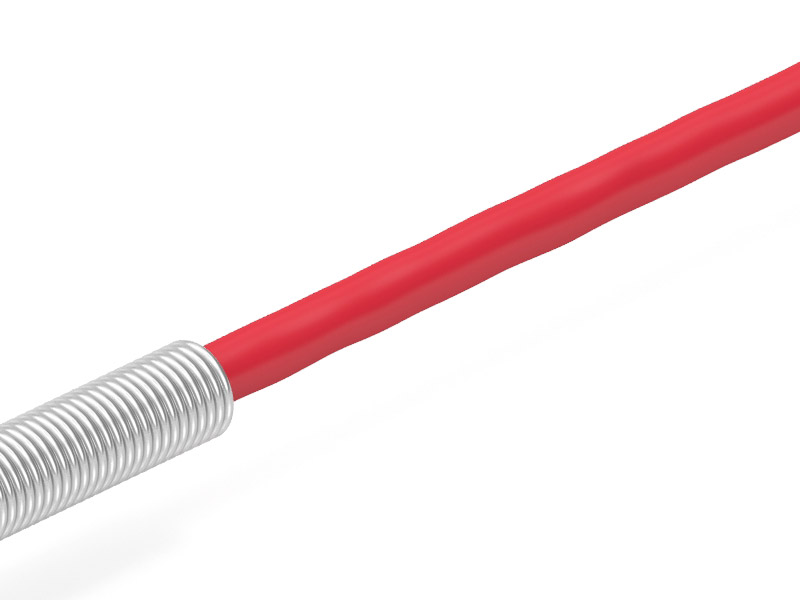
Calibration included
The LLB350 has been tested by FUTEK’s world-class calibration department and is NIST traceable. We can also reduce hidden costs and setup time by calibrating your sensor with FUTEK electronics of your choice. In addition, we offer calibration to ANSI Z540-1 and ISO 17025 standards upon request.
Made in Irvine, CA
Designed and manufactured in-house. Our multidisciplinary engineering teams, high precision machining center, state-of-the-art quality assurance systems, and R&D and manufacturing facilities are all under one roof, allowing us to continuously reinvent and refine our products and processes.