Donut/Through Hole Load Cell

Robust and accurate with high resistance to off-axis loads
Description
Model LTH350 is a Through Hole Donut/Washer Load Cell built for press or inline compression applications. The standard LTH350 Donut Load Cell model has a very robust construction available in 17-4 Stainless Steel, with an I.D. range of 1/4" [6.5 mm] to 5/8" [16.1 mm], as well as a 4 Pin Micro Receptacle for simplified assembly. You will also find options for external matched output readily available.
The Donut Load Cell offers high accuracy and high stiffness. It has nonlinearity of ±0.5%, deflection of 0.002” [0.05 mm] nominal and operating temperature of -60 to 200° F [15 to 75° C]. The standard LTH350 Washer Load Cell can be modified or customized to meet your requirements and most capacities are in our inventory, making them available for 24-hour shipping.
Product Highlights And Features
- Fast response time
- Quick Connect/Disconnect Receptacle
- Compatible in load washer applications
- Offered in a variety of capacities and inner diameters
- Low power consumption
LTH350 is a miniature, low-profile donut or through-hole load cell for applications that require the load structure to pass through the sensor. It features multiple strain gauges that optimize the model’s performance and significantly reduces the influence of extraneous loads.
LTH350 is ideal for inline applications with limited space that require a sensor that can handle eccentric loads and still maintain a high level of accuracy and reliability. It features an integrated 4-pin micro connector for easy cable connection and disconnection. This model can also be modified to suit OEM applications. FUTEK offers application and engineering resources during DFM/DFX stage upon request.
Small footprint
At 0.5in (12.7mm) height and 1.48in (37.6mm) diameter, these miniature sensors fit into applications that require a very small footprint. The units are offered in a variety of inner diameter sizes from 1/4in to 5/8in (6.35 to 15.9mm). The lightweight models weigh 3.5oz (99g).
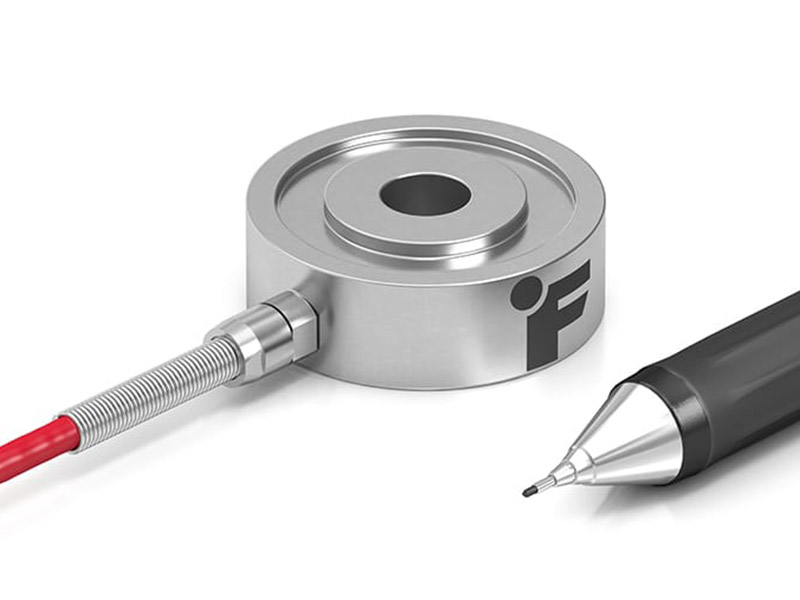
Powerful performance
The proprietary design, coupled with FUTEK’s sophisticated metal foil strain gauge technology, guarantees high accuracy and repeatability. The extra strain elements inside the sensor ensures high sensitivity and accurate measurements to off-axis loads, even in high extraneous load conditions. This allows you to mount the sensor in different rotational patterns, orienting the sensors to suit your system design, and still collect reliable, and accurate measurements.
Robust construction
The sensors are conformally coated inside with a silicone dielectric gel, which absorbs shock and vibration, ensuring that the interconnected wires do not fatigue or fail. The coating also provides environmental protection against any ingress, improving product life. Welded isolation diaphragms add another level of robustness and protection against outdoor or washdown environments. The overall design qualifies for IP64 rating.
Through-hole mounting
LTH350 model has a through hole with an inner hub that allows the load to be attached. The outer diameter has a hub on the bottom base, where the unit is to be supported. The diaphragm between the loading point (ID) and the mounting point (OD) is where the strain is measured. Typically, a bolt or any other component connected to the load passes through the ID.
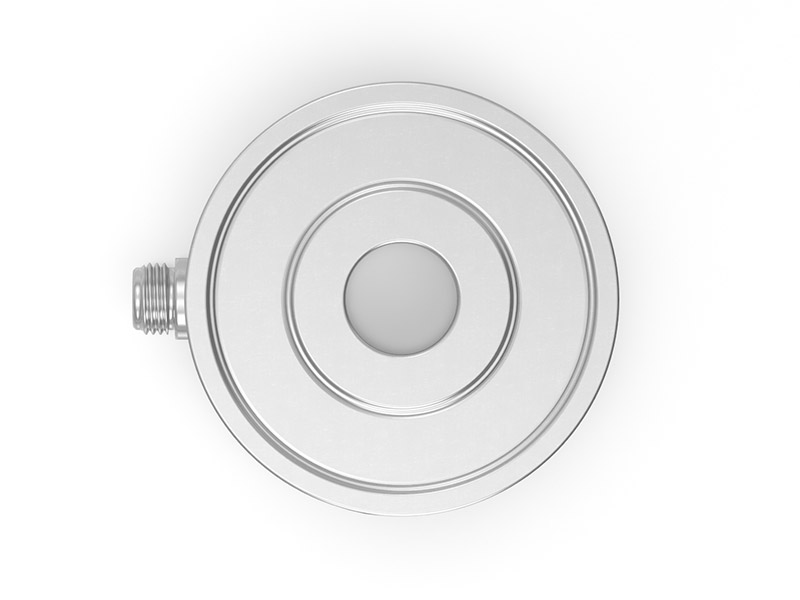
Plug in, plug out
The LTH350 is now offered with an integrated 4-pin micro connector, which allows for easy and simple cable connection and disconnection. A damaged sensor cable can be replaced without having to replace or disassemble the sensor or any other system component, which saves time, leads to higher system availability, and reduces the total cost of ownership. It also simplifies the installation process, reducing installation time and maximizing up time.
Best-in-class materials
The exceptional quality of LTH350 makes it highly durable, robust, and reliable. Its body is made of aerospace-grade 17-4PH stainless steel, which provides high strength, high hardness, and corrosion resistance over a wide temperature range.
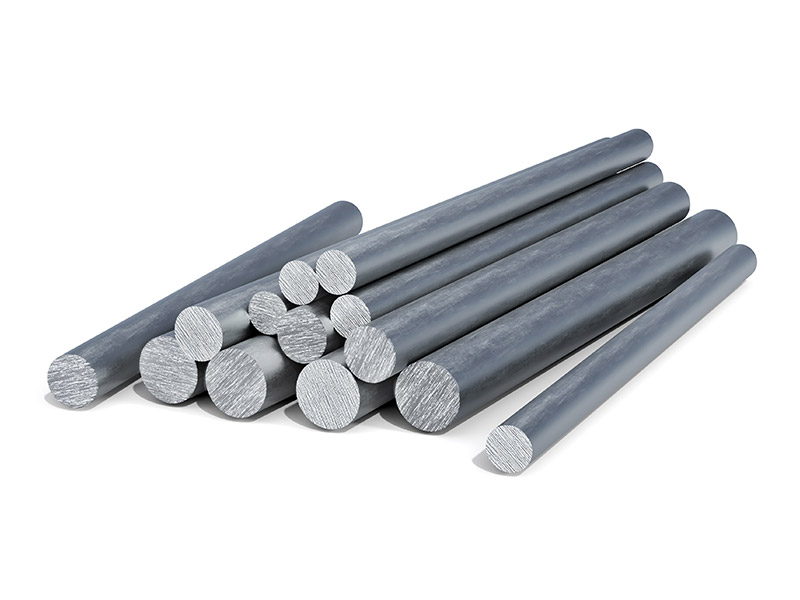
Recommended applications
FUTEK’s LTH series sensors are ideally suited for applications such as press, inline compression applications, bolt fastening, toggle force clamp measurement, overload monitoring, post or leg mount, rolling mill systems, nut runner force/torque monitoring, and dual tank level controllers. Being miniature, highly robust, and reliable, these sensors are featured in NASA’s Orion deployment mechanism.
Calibration included
The LTH350 has been tested by FUTEK’s world-class calibration department and is NIST traceable. We can also reduce hidden costs and setup time by calibrating your sensor with FUTEK electronics of your choice. In addition, we offer calibration to ANSI Z540-1 and ISO 17025 standards upon request.
Made in Irvine, CA
Designed and manufactured in-house. Our multidisciplinary engineering teams, high precision machining center, state-of-the-art quality assurance systems, and R&D and manufacturing facilities are all under one roof, allowing us to continuously reinvent and refine our products and processes.

Robust and accurate with high resistance to off-axis loads
Description
Model LTH350 is a Through Hole Donut/Washer Load Cell built for press or inline compression applications. The standard LTH350 Donut Load Cell model has a very robust construction available in 17-4 Stainless Steel, with an I.D. range of 1/4" [6.5 mm] to 5/8" [16.1 mm], as well as a 4 Pin Micro Receptacle for simplified assembly. You will also find options for external matched output readily available.
The Donut Load Cell offers high accuracy and high stiffness. It has nonlinearity of ±0.5%, deflection of 0.002” [0.05 mm] nominal and operating temperature of -60 to 200° F [15 to 75° C]. The standard LTH350 Washer Load Cell can be modified or customized to meet your requirements and most capacities are in our inventory, making them available for 24-hour shipping.
Product Highlights And Features
- Fast response time
- Quick Connect/Disconnect Receptacle
- Compatible in load washer applications
- Offered in a variety of capacities and inner diameters
- Low power consumption
LTH350 is a miniature, low-profile donut or through-hole load cell for applications that require the load structure to pass through the sensor. It features multiple strain gauges that optimize the model’s performance and significantly reduces the influence of extraneous loads.
LTH350 is ideal for inline applications with limited space that require a sensor that can handle eccentric loads and still maintain a high level of accuracy and reliability. It features an integrated 4-pin micro connector for easy cable connection and disconnection. This model can also be modified to suit OEM applications. FUTEK offers application and engineering resources during DFM/DFX stage upon request.
Small footprint
At 0.5in (12.7mm) height and 1.48in (37.6mm) diameter, these miniature sensors fit into applications that require a very small footprint. The units are offered in a variety of inner diameter sizes from 1/4in to 5/8in (6.35 to 15.9mm). The lightweight models weigh 3.5oz (99g).
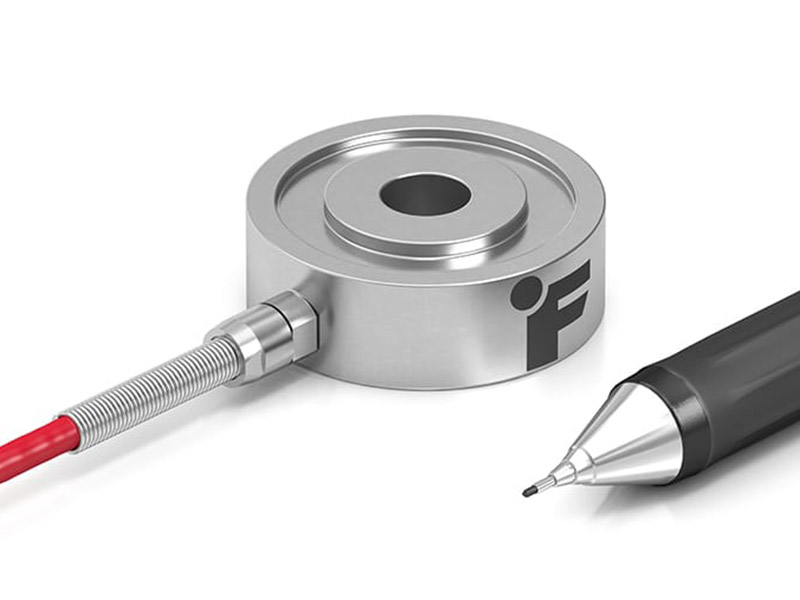
Powerful performance
The proprietary design, coupled with FUTEK’s sophisticated metal foil strain gauge technology, guarantees high accuracy and repeatability. The extra strain elements inside the sensor ensures high sensitivity and accurate measurements to off-axis loads, even in high extraneous load conditions. This allows you to mount the sensor in different rotational patterns, orienting the sensors to suit your system design, and still collect reliable, and accurate measurements.
Robust construction
The sensors are conformally coated inside with a silicone dielectric gel, which absorbs shock and vibration, ensuring that the interconnected wires do not fatigue or fail. The coating also provides environmental protection against any ingress, improving product life. Welded isolation diaphragms add another level of robustness and protection against outdoor or washdown environments. The overall design qualifies for IP64 rating.
Through-hole mounting
LTH350 model has a through hole with an inner hub that allows the load to be attached. The outer diameter has a hub on the bottom base, where the unit is to be supported. The diaphragm between the loading point (ID) and the mounting point (OD) is where the strain is measured. Typically, a bolt or any other component connected to the load passes through the ID.
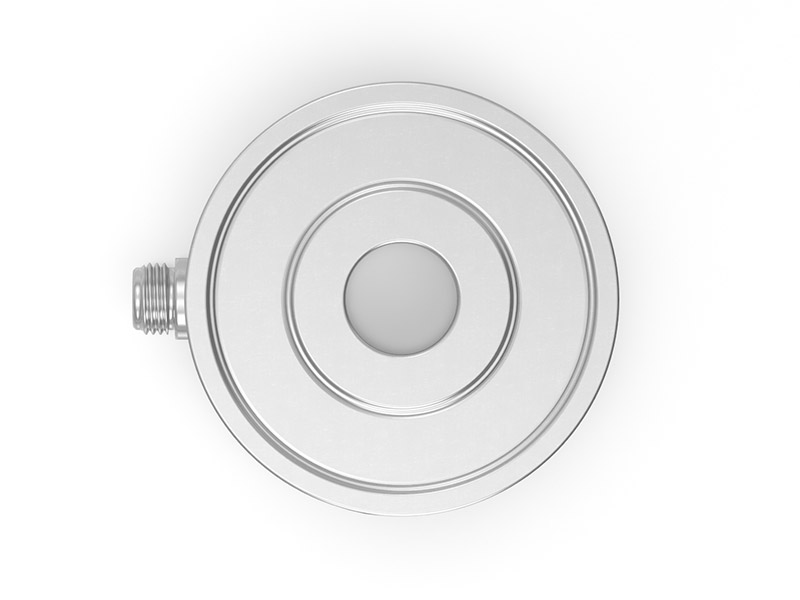
Plug in, plug out
The LTH350 is now offered with an integrated 4-pin micro connector, which allows for easy and simple cable connection and disconnection. A damaged sensor cable can be replaced without having to replace or disassemble the sensor or any other system component, which saves time, leads to higher system availability, and reduces the total cost of ownership. It also simplifies the installation process, reducing installation time and maximizing up time.
Best-in-class materials
The exceptional quality of LTH350 makes it highly durable, robust, and reliable. Its body is made of aerospace-grade 17-4PH stainless steel, which provides high strength, high hardness, and corrosion resistance over a wide temperature range.
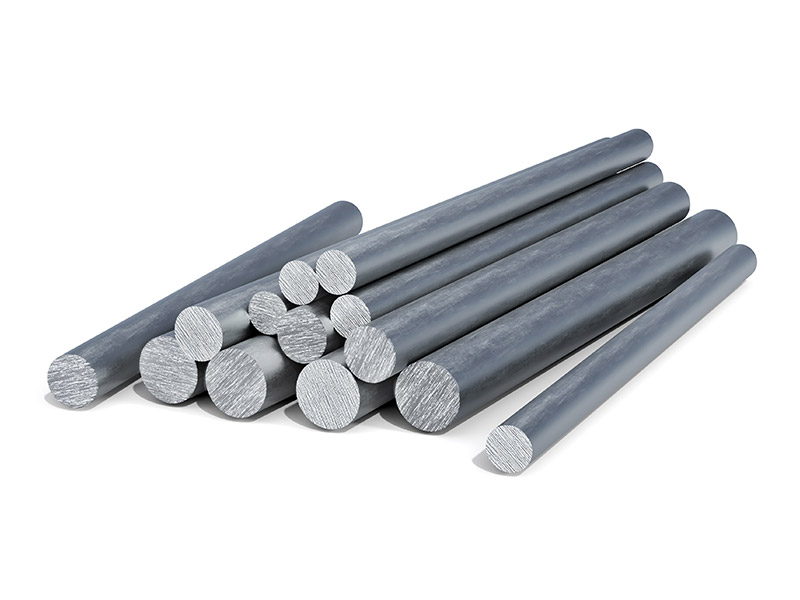
Recommended applications
FUTEK’s LTH series sensors are ideally suited for applications such as press, inline compression applications, bolt fastening, toggle force clamp measurement, overload monitoring, post or leg mount, rolling mill systems, nut runner force/torque monitoring, and dual tank level controllers. Being miniature, highly robust, and reliable, these sensors are featured in NASA’s Orion deployment mechanism.
Calibration included
The LTH350 has been tested by FUTEK’s world-class calibration department and is NIST traceable. We can also reduce hidden costs and setup time by calibrating your sensor with FUTEK electronics of your choice. In addition, we offer calibration to ANSI Z540-1 and ISO 17025 standards upon request.
Made in Irvine, CA
Designed and manufactured in-house. Our multidisciplinary engineering teams, high precision machining center, state-of-the-art quality assurance systems, and R&D and manufacturing facilities are all under one roof, allowing us to continuously reinvent and refine our products and processes.